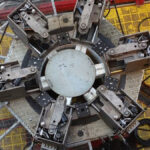
Torque Calibration Frequency: Industry Guidelines and Recommendations
February 13, 2025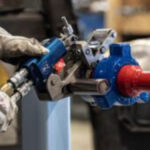
15 Tips for Hydraulic Tools Safety
February 13, 202510 Best Practices for Torque Tool Storage and Care
Torque tools are essential for precision work, ensuring safety and accuracy across various industries. However, their effectiveness depends largely on how well they’re maintained and stored. Neglecting proper care can lead to calibration issues, reduced performance, and even costly replacements.
Keep reading to learn the 10 best practices for torque tool storage and care. These tips will protect your investment, extend your tools’ lifespan, and maintain peak performance, keeping your torque tools in excellent working condition for years to come.
1. Store at Minimum Settings
Proper usage of your torque tools is critical, but how you store them is equally important in maintaining their accuracy and performance over time.
Storing a torque wrench at a fully loaded setting can put undue stress on the internal spring, potentially causing it to weaken or lose calibration. Conversely, completely off-loading the spring during storage can lead to unwanted movement of internal components, which may affect the tool’s precision in the future.
The best practice? Always wind your torque wrench down to its minimum setting before storing it for extended periods. This is an essential practice in torque tool storage that helps preserve the spring tension and ensures your tool remains accurate and ready for use when you need it.
2. Keep Tools Clean
Keeping your torque tools clean is vital for maintaining their accuracy and functionality. After each use, make it a habit to clean your tools thoroughly, removing dirt, grease, and debris that can interfere with their performance. Use mild cleaning agents specifically recommended by the manufacturer; harsh chemicals can damage sensitive components and lead to costly repairs.
Pay special attention to hydraulic connections and moving parts during your cleaning process. These areas are prone to build-up, which can impair performance and cause tools to operate unpredictably. Establish a routine cleaning schedule to guarantee you’re consistently maintaining peak tool functionality.
3. Ensure Proper Storage for Torque Wrenches
Protective cases for your torque tools are crucial for safeguarding their performance and extending their lifespan. These protective cases shield your tools from dust, moisture, and physical impacts, greatly enhancing longevity and operational efficiency.
Storing torque wrenches in protective cases prevents accidental drops and damage during transport, which could lead to inaccurate torque applications—something no skilled technician can afford.
Many manufacturers design protective cases with custom foam inserts to keep tools securely in place and prevent internal components from shifting. This not only protects your tools but also helps maintain their calibration. Additionally, environmental factors can lead to wear or misalignment, so storing your tools in protective cases is essential to keep them reliable and accurate.
4. Perform Regular Inspections
Regular inspections ensure your torque tools remain in top working condition. By routinely checking for signs of wear and tear, you can identify potential issues before they escalate into costly repairs or tool failure.
Here are some inspections you should perform.
- Look for visible damage that could impact the tool’s performance, such as cracks, deformations, or loose components.
- Check the ratchet mechanism to ensure it moves smoothly. Stiffness or uneven motion could mean it needs maintenance or might fail.
- Don’t overlook the moving parts—ensure they function correctly and are debris-free. Blockages can severely compromise torque application and shorten the tool’s lifespan.
Additionally, periodic adjustments are necessary to ensure the tool delivers accurate torque. The frequency of repairs and calibrations will depend on how often the tool is used and the manufacturer’s guidelines. So, make sure you follow the recommended torque tool maintenance and calibration schedules.
5. Follow Lubrication Guidelines
Following the lubrication guidelines is essential to guaranteeing your torque tools perform at their best over time. Always use manufacturer-recommended lubricants to ensure compatibility and peak performance of your tool’s moving parts. Regular lubrication reduces friction, which enhances the tool’s longevity and efficiency. Neglecting this critical step can lead to increased wear and potential malfunctions you want to avoid.
Stick to the lubrication intervals outlined in your user manual to maintain consistent operation and prevent unnecessary breakdowns. Focus on key components, such as ratchet mechanisms and hydraulic connections, where smooth functionality is imperative. Applying lubricant to these areas ensures your tools operate seamlessly under demanding conditions.
6. Inspect Hydraulic Fluid
Proper hydraulic fluid maintenance is crucial for operating your hydraulic torque wrench at its best. Regularly check fluid levels to ensure they stay within the recommended range, as low or contaminated fluid can significantly reduce performance. Always use high-quality hydraulic fluid compatible with your wrench to maintain efficiency and prevent damage.
It’s also crucial to replace the fluid at the intervals specified by the manufacturer to keep your tool in top condition. Use the correct grade and type of hydraulic fluid to prevent internal damage and ensure smooth, reliable operation over time. Regular fluid maintenance is key to extending the lifespan of your hydraulic wrench and optimizing its performance.
7. Calibrate Periodically
Regular calibration intervals are necessary to maintain the accuracy of your torque wrench, especially in industries that demand consistent precision. This practice helps prevent issues like over-tightening or under-tightening, which can compromise the integrity of mechanical joints.
Two key standards set by the International Organization for Standardization (ISO) govern the calibration frequency of torque wrenches: ISO 6789-1:2017 and ISO 6789-2:2017. These guidelines recommend testing torque tools for calibration every 5,000 cycles or six months, whichever occurs first. If a tool is out of calibration, it must undergo recalibration, retesting, and recertification. To prevent future inaccuracies from going undetected, the calibration interval for that tool is subsequently reduced to 2,500 cycles or three months.
8. Use Manufacturer-Approved Accessories
Using the right accessories is critical for achieving accurate torque applications and maintaining your tool’s optimal performance. Manufacturers design specific accessories, like extensions or adapters, that are made to work seamlessly with their torque tools. Using unauthorized accessories can compromise accuracy and potentially cause damage to your tool.
It’s always best to stick to manufacturer-recommended accessories and avoid aftermarket options that may not be compatible or meet quality standards. If you need to replace any parts, choose genuine spare parts from the manufacturer or reputable suppliers for proper fitment and performance. Using non-approved accessories might seem like a cost-saving measure, but it could lead to expensive repairs or replacements in the long run.
9. Use Proper Handling Techniques
Proper handling is essential for preserving the accuracy and longevity of your torque tools. Always handle them with care, avoiding sudden drops or impacts that could affect their calibration and functionality. When not in use, store your torque wrenches in protective cases to safeguard them from dust, moisture, and physical damage, helping to prolong their lifespan and maintain precise measurements.
For added protection, transport your torque tools in padded cases or bags to prevent movement and minimize the risk of damage during transit. Avoid exposing the tools to extreme temperatures and humidity, as these conditions can cause corrosion and affect internal components. Regularly inspect your torque tools for signs of wear or damage before and after each use to ensure they’re ready for accurate torque application.
10. Document Maintenance Records
Keeping maintenance records is a best practice in any industry, and it’s no different when it comes to torque tools. Documenting torque tool maintenance tasks like repairs, lubrication schedules, and calibrations helps you monitor your tool’s performance and identify potential issues early on.
By recording the dates and specifics of these tasks, you can spot patterns of wear and potential issues before they become serious problems, allowing for timely interventions that extend the lifespan of your tools.
Be sure to include specific details in your torque tool maintenance logs, such as the type of lubricants used and any adjustments made. This thorough documentation aids in troubleshooting and provides a valuable reference for future maintenance. Regularly updating your records ensures compliance with industry standards and demonstrates your commitment to maintaining the quality and longevity of your torque tools.
Final Thoughts
Following these 10 best practices for torque tool storage and care will significantly enhance the longevity and performance of your tools. From proper storage for torque wrenches to routine inspections and using only manufacturer-approved accessories, these simple steps help maintain your tools’ accuracy and reliability.
When you need precision and reliability in bolting applications, TorqLite is your trusted partner for industrial torque solutions. Whether you’re in construction, mining, oil & gas, power plants, or wind energy, we provide the tools you can count on to get the job done right. With TorqLite, you’ll have the accuracy, durability, and performance needed to tackle every challenge with confidence. Contact us today!