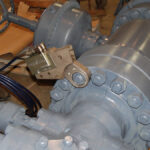
How to Select the Right Torque Wrench for Heavy Equipment Maintenance
February 13, 2025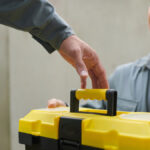
10 Best Practices for Torque Tool Storage and Care
February 13, 2025Torque Calibration Frequency: Industry Guidelines and Recommendations
One of the most important factors to consider when ensuring the accuracy and safety of torque tools is torque calibration frequency. Proper calibration guarantees precise measurements, extends your equipment’s lifespan, reduces costly errors, and maintains compliance with industry standards.
However, determining the right calibration interval can be tricky, as it depends on various factors such as usage frequency, environmental conditions, and the type of equipment.
In this blog, we’ll take a look at industry guidelines and expert recommendations to help you establish the optimal torque calibration frequency for your operations.
When to Calibrate Torque Wrenches?
BS EN ISO 6789:2017 suggests calibrating your torque wrench every 12 months or after every 5,000 operations, whichever comes first. However, the calibration frequency should be based on the criticality of the work being performed. High-risk industries such as aerospace, automotive, and energy may require more frequent calibrations, as even small inaccuracies can lead to significant consequences. More frequent checks may be necessary if a torque tool shows signs of malfunction or has a history of calibration issues.
If your torque wrench has been in storage for an extended period, it’s wise to calibrate it before using it again. Environmental factors, such as temperature fluctuations during storage, can impact its accuracy, even if properly calibrated beforehand.
Additionally, always check the manufacturer’s recommendations regarding calibration frequency, especially if you use a specialized or high-precision wrench.
Importance of Torque Calibration
The importance of torque calibration cannot be overstated, as it affects your work’s quality and safety. Here are some reasons why regular calibration is crucial:
- Consistency and Quality Assurance: Torque calibration guarantees that tools consistently meet exact torque requirements, resulting in higher quality products and processes.
- Enhanced Safety: Properly calibrated torque tools prevent over or under-tightening, reducing the risk of accidents and injuries.
- Time and Cost Savings: Regular calibrations ensure accurate and reliable measurements, reducing errors and costly rework.
- Accuracy and Reliability: Frequent torque calibration ensures your tools are accurate and reliable, avoiding measurement errors and potential product failures.
- Extended Lifespan of Tools: Regular calibration extends the life of your torque tools, ensuring they remain in optimal working condition.
- Risk Mitigation and Compliance: In industries where precision is critical, frequent calibrations are essential to prevent costly errors and maintain compliance with safety standards.
Factors That Impact Torque Calibration Frequency
While there are standard torque calibration recommendations, the calibration frequency isn’t one-size-fits-all and depends on several factors specific to your operations.
Here are key factors to consider when determining the calibration frequency for your torque wrench:
- Frequent use plays a significant role in calibration needs; if the torque wrench is used daily, it will require more frequent calibration than a tool used intermittently.
- If the torque wrench is dropped or banged against a hard surface, it may lose accuracy and require immediate calibration.
- Environmental factors, such as exposure to extreme temperatures, humidity, or moisture, can negatively impact the wrench’s performance and require more frequent checks.
- The nature of the work being performed is crucial; high-stakes industries, such as aerospace or automotive, demand more frequent calibration due to the critical nature of the tasks.
- The quality and design of the torque wrench affect how long it retains its calibration; higher-end models tend to maintain accuracy for longer periods than lower-quality tools.
- Any signs of wear, damage, or inconsistency in readings should prompt immediate recalibration to ensure the wrench is functioning correctly.
- The level of maintenance the torque wrench has received over time also impacts calibration frequency; a poorly maintained tool is more likely to require frequent recalibration.
Where to Get a Torque Wrench Calibrated?
To ensure accurate and reliable calibration, it’s essential to get your torque wrench calibrated by a certified and reputable service provider.
Some options for calibration include:
- In-House: You can calibrate your torque wrench in-house if you have the necessary expertise and equipment. This option may be suitable for lower-risk industries or those with a limited number of torque tools.
- Third-Party Calibration Labs: Send your torque tools to accredited third-party labs. These labs should be certified under ANSI/NCSL-Z540, ISO, or the National Institute of Standards and Technology (NIST).
- Manufacturer Calibration Services: You can also get your torque wrench calibrated by the manufacturer. This option is ideal if you use specialized or high-end tools, as the manufacturer knows its products well and can calibrate them correctly.
Final Thoughts
Regularly calibrating your torque wrench ensures precision and safety in your work. While there are industry guidelines and expert recommendations, knowing when to calibrate torque wrenches ultimately boils down to understanding your specific operations’ criticality and considering various factors that impact calibration frequency.
When precision and performance matter most, you can count on TorqLite for industry-leading torque solutions tailored to your needs. We are committed to providing innovative, high-performance solutions to meet your bolting needs. Learn how our advanced tools and services can help you achieve precision and efficiency in every project. Contact TorqLite today!